Residual Sodium Check During Clean-in-Place Process
Caustic soda or sodium hydroxide (NaOH) is the chemical commonly used in alkaline cleaning solution for clean-inplace (CIP) in process plants. Measuring the sodium ion concentration on the water rinse or swab can indicate whether residual chemical has been removed properly from the process equipment.
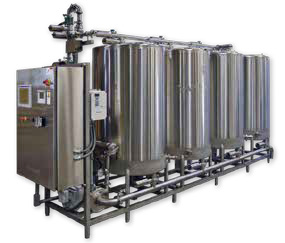
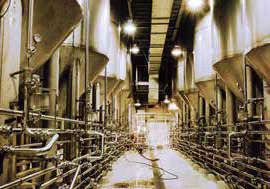
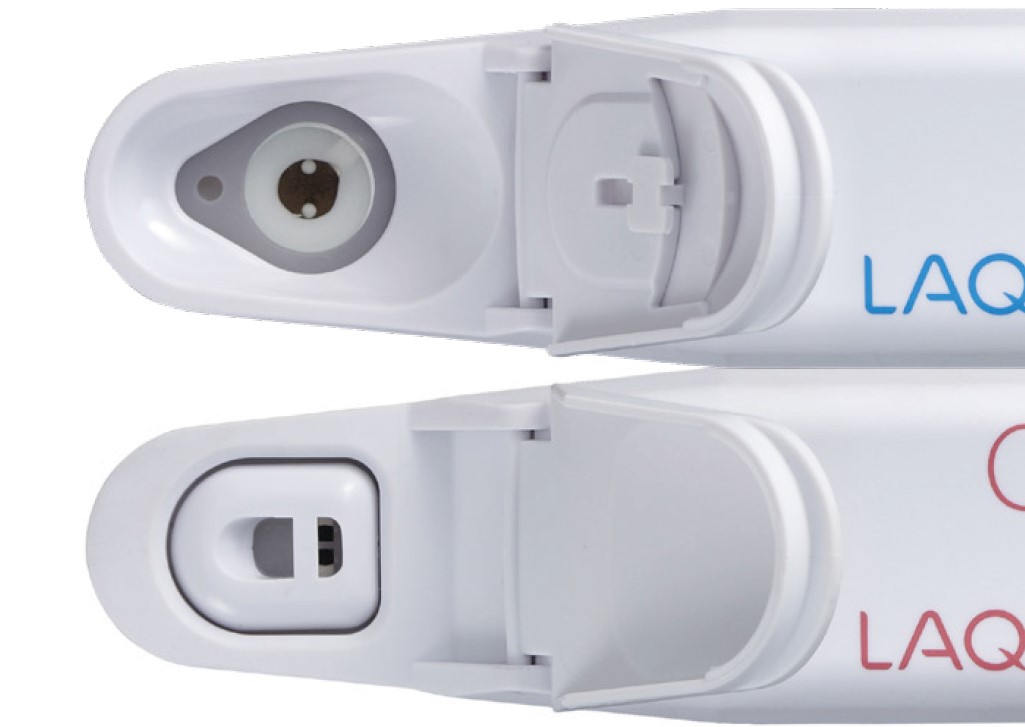
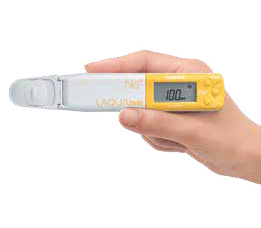
Introduction
Clean-in-place (CIP) is a method of cleaning the interior surfaces of pipes, vessels, process equipment, filters and associated fittings without disassembly. The CIP system is run by digital computer called programmable logic controllers (PLCs) to control the flow, temperature, and time for the chemical solutions, which could be acidic, alkaline or sometimes both, to achieve maximum cleaning. The chemical solutions are circulated through a circuit of tanks and/or lines to eliminate contaminants or product residues and are rinsed out with water. Depending on the CIP system, chemical solutions may flow back to a reservoir so that they can be re-used or drained immediately after they have been used.
After CIP, the equipment should be visibly clean and free from chemical residues. The final water rinse must ensure that chemical residues are removed properly. Chemical residues from cleaning solutions can be monitored by specific or non-specific analytical method. Specific methods that detect the individual ingredients of cleaning solutions are ion selective electrode (ISE), high performance liquid chromatography (HPLC), thin layer chromatography (TLC), flame photometry, and ultraviolet spectroscopy. Non-specific methods that detect the presence of blend of ingredients are pH, conductivity, and total organic carbon (TOC). Specific methods are usually preferable by regulatory agencies, but they may accept non-specific methods with adequate rationales for their use.
As CIP offers fast, repeatable, and effective cleaning without chemical exposure risk to people, it is utilized in industries that require high levels of hygiene such as dairy, beverage, processed foods, pharmaceutical, and cosmetics. CIP is typically employed for cleaning bioreactors, fermenters, mix vessels and other equipment in manufacturing facilities and many CIP systems use alkaline cleaning solutions containing 0.5 to 2% (by weight) caustic soda or sodium hydroxide (NaOH) to remove fats and proteins.
The LAQUAtwin B-722 or Na-11 sodium ion meter can be used to measure and monitor residual sodium ion (Na+) concentration during CIP in process plants. The meter analyses as little as 0.3 ml sample and delivers result in just few seconds. This fast, easy, and accurate measurement complements the cleaning efficiency of CIP.
Method
Calibrate the LAQUAtwin B-722 or Na-11 sodium ion meter according to manufacturer’s instructions using the 150ppm and 2000ppm sodium ion standards included in the kit.
Sample Measurement
Rinse water sampling and wipe sampling are two sampling methods for measuring cleaning chemical residues. Combination of these is desirable.
Rinse water sampling involves taking a sample of an equilibrated water rinse (usually water for injection or pure water) that has been recirculated over all surfaces. To measure, place drops of rinse water sample onto the sodium ion sensor using a pipette. Alternatively, open the sensor guard and soak the sensor into a beaker containing rinse water.
Swab or wipe sampling is done directly on equipment surfaces. This is performed in order to assure that the residues are being adequately detected and not simply sitting on the surface and not being dissolved into the equilibrated rinse water. Before wiping begins, allow the equipment to dry after the cleaning procedure and moisten the sampling sheet included in the meter kit with water for injection or pure water. To measure, wipe the surface with a moistened sampling sheet then place it onto the sensor. A blank preparation is required for this sampling method.
Refer to Technical Tip 2: LAQUAtwin Ion Sensor Maintenance Procedures for detailed information on conditioning, cleaning, and storing the sodium ion sensor. The technical tip can be downloaded from the support section of our website www.horiba-laqua.com.
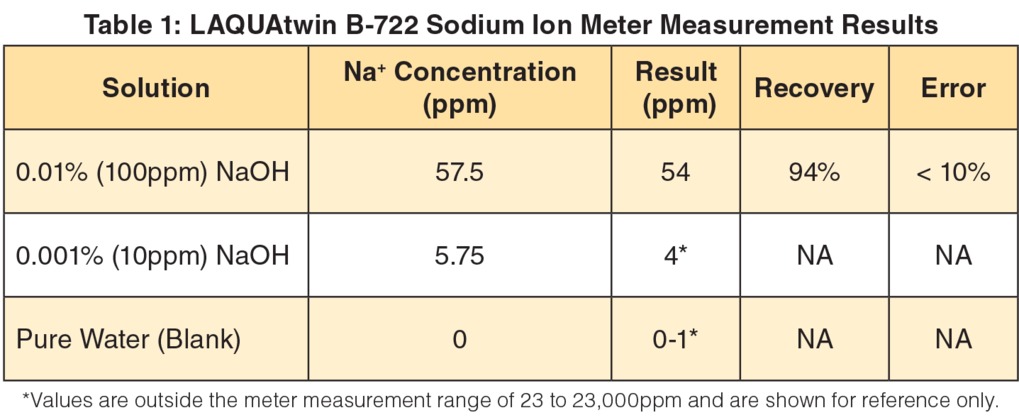
Results and Benefits
Cleaning validation is a critical part of current good manufacturing practice to ensure that production materials that come in contact with equipment surfaces are not contaminated. The pre-rinse, alkali circulation, and other steps must take place in correct order. Checks on the identity, purity and strength of cleaning chemicals and on quality of water used for rinsing are needed. Also, the validation protocol must include testing for the residual cleaning chemical to ensure that cleaning chemical used is properly removed. The analysis must be quantitative and the acceptance criteria are determined according to regulatory guidelines and company policy. The table above shows the measurement results of LAQUAtwin B-722 sodium ion meter.
References And Suggested Readings
- Batt, C.A., Modern Systems of Plant Cleaning. Encyclopedia of Food Microbiology, pp 194-199.
- Chan, C.C., Lam, H., Zhang X., Practical Approaches to Method Validation and Essential Instrument Qualification.
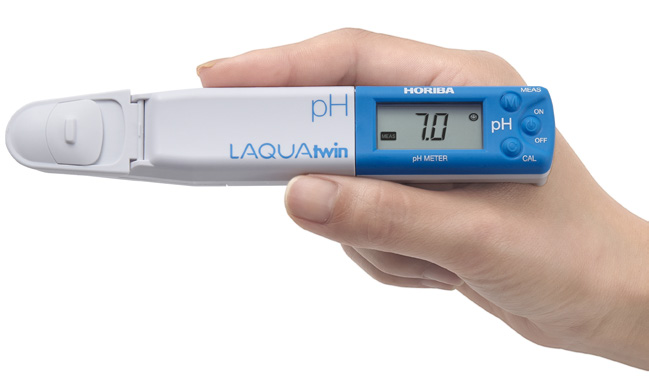
LAQUAtwin: the only meters with flat sensor technology.
HORIBA’s highly-sensitive, flat sensor technology opens up new possibilities for sampling and sample types. Only a small amount of sample is required, so you can easily sample in situ without the need for beakers or other labware. Sensors are easily replaced as required.
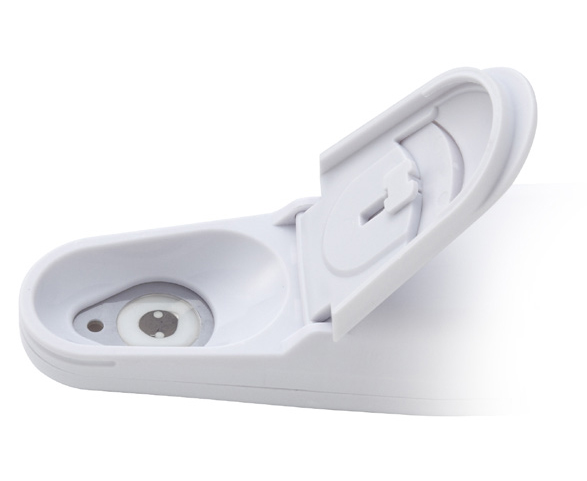
Calibrate and measure at the touch of a button — the smiley face will tell you when the result can be read.
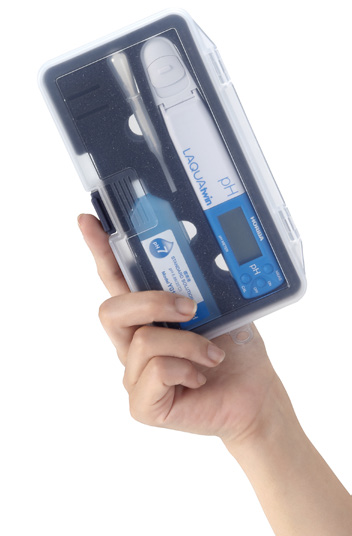
LAQUAtwin is fully waterproof and dustproof.
The meter and sensor are fully waterproof* and dustproof, so you can take it anywhere.
* IP67 rated. Will withstand immersion for 30 minutes at 1 m. Not suitable for underwater use.
Carry case comes as standard for handy portability.
The compact carry case contains everything you need for your measurements, including the standard solution and sampling sheets.